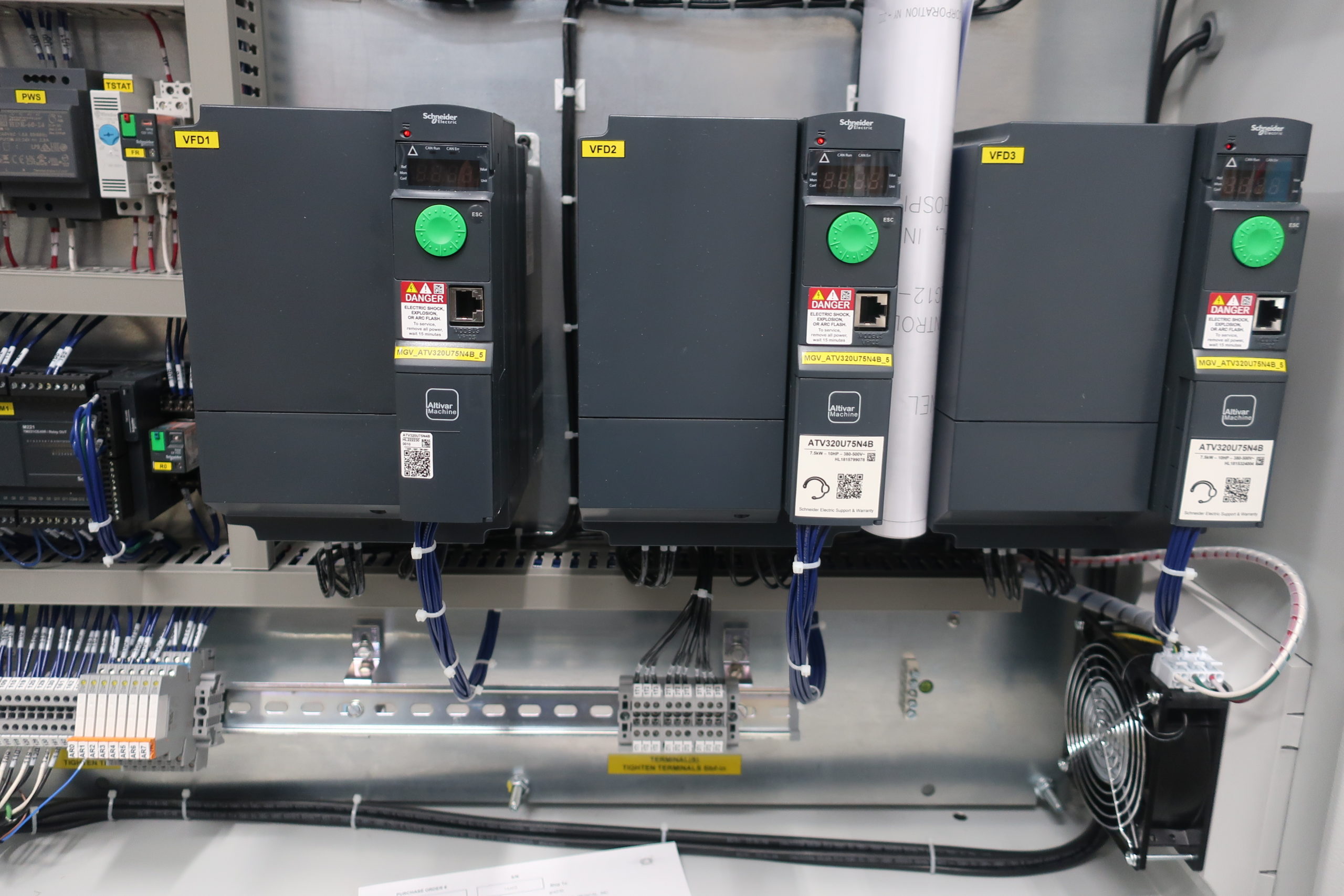
Use of VFD in Medical Vacuum Control Panel
One of the notable technological advancements in recent years is the integration of Variable Frequency Drives (VFDs) into medical vacuum control panels. The primary purpose of using a VFD is to save energy by reducing peak demand charges, eliminating hard start/stop cycles, and aligning pump performance with the actual demand of the hospital. Axecon manufactures VFD panels for a variety of industries and features a dedicated product page that highlights the full range of benefits offered by VFD panels.
While VFD technology is highly effective, its successful implementation is crucial to fully realize the potential energy savings and operational efficiency it offers.
Sharing a Single VFD Between Pumps
The cost of adding a Variable Frequency Drive (VFD) to a medical vacuum panel can be quite significant. As manufacturers work to reduce product costs, some performance trade-offs are often necessary to achieve this goal. The use of a single VFD in medical applications is quite common, and the savings are easily noticeable. In a non-VFD duplex panel, the power circuit would typically include two motor starters (contactors and combined overload protection). Upgrading to a panel with a single VFD requires adding another set of contactors, but only one VFD is needed for this application.
Since NFPA 99 requires the system to be sized with one pump on reserve, the pump will always operate under the VFD, unless the lag pump is activated. Ideally, the lag pump should rarely need to run, making this an ideal design for a single VFD setup. However, as the system scales up to triplex and larger configurations, the energy savings diminish, and the benefits of using a single VFD start to fade.
In triplex systems and larger, the demand typically involves all pumps except one. When the vacuum level drops, the first pump will engage as a VFD-operated pump, providing the energy savings mentioned earlier. As the demand continues to rise, however, the second pump will need to be activated. At this point, the second pump must run at full speed, as it is no longer controlled by the VFD. Consequently, the energy savings previously achieved are no longer applicable to this pump, since it is now operating as a direct-driven unit.
This issue becomes even more pronounced as additional pumps are added to the system, as more pumps will operate at full speed without the benefits of VFD control, further diminishing the overall energy savings and performance advantages.
Extra Point of Failure
The design of a single VFD system requires that the VFD be shared between pumps, with each pump having two sets of contactors: one for direct drive when it is operating as a reserve or lag pump, and one for VFD drive. This setup ensures that only one pump is controlled by the VFD at a time, isolating the others to prevent simultaneous operation under VFD control.
In a triplex configuration, this results in a total of six contactors—each pump having two—plus the VFD itself. Each of these contactors is a potential point of failure, adding complexity to the system. The increased number of components, combined with the VFD, makes these types of systems more difficult to maintain and diagnose. Troubleshooting can become more challenging, as failures could occur at multiple points in the system, requiring more time and effort to identify and resolve the issue.
Solutions? Multi VFD
The optimal way to fully leverage VFD technology is to apply a VFD to each pump in the system. By doing so, you significantly enhance the energy savings and reduce the number of potential points of failure. With each pump operating independently on its own VFD, the peak demand charge is consistently lower, delivering the full energy savings that the VFD technology is designed to provide.
Additionally, by assigning a dedicated VFD to each pump, the need for contactors and overload protection is eliminated. This is because each VFD inherently provides overload protection for its respective pump, streamlining the design and reducing the complexity of the system.
While the cost difference between a single VFD and multiple VFDs may seem significant at first glance, the increase is often quite small when considering the savings in other components, such as contactors and overload relays. Manufacturers typically offset this additional cost by not having to install these other components, making the multi-VFD solution more cost-effective in the long run while also improving reliability and performance.
Axecon's 5000 Series Control Panel offers an industry-leading multi-VFD solution for contactless claw vacuum operation. With each VFD dedicated to a specific pump, the reliability of these panels far exceeds that of single VFD control panels. This design not only enhances performance but also ensures greater system longevity and efficiency.
Whether you're looking for a new system or a replacement control panel, our team is ready to assist you in selecting the right VFD application for your medical vacuum system. Reach out to us today, and we'll help you implement a solution that meets your needs for both reliability and energy savings.